Both IGCT and GTO (the source of IGCT) are controlled by gate signals and can withstand high di/dt rates, which means that most applications do not require buffers. In IGCT, the gate current required to turn off the device is higher than the anode current. The combination of high gate current and high di/dt ratio means that traditional interconnections cannot be used to connect IGCTs to gate drivers. On the contrary, the gate drive PCB and IGCT are delivered as0ne unit. The gate driver is surrounded by a large circular conductor connected to the edge of the IGCT. The large contact area and extremely short connection distance reduce the inductance and resistance of the gate connection,
Like most thyristors, IGCT is manufactured as a single wafer (Figure 4). This is in contrast to the IGBT manufactured as a series of cells. The structure of each cell is similar to the n-channel vertical Power MOSFET, except that the p+collector layer replaces the n+drain and forms a vertical PNP bipolar junction transistor. The gate structure and driving topology of IGCT support much faster turn-off time than GTO. GTO is usually limited to operating at 500 Hz, while IGCT can operate at frequencies up to a few kHz in a short period of time, with a maximum switching frequency of 500 Hz in the long term. The rated breaking current of IGCT is 520 to 5000 A, and typical blocking voltage ratings are 4500, 5500, and 6500 V. They are used for industrial and traction drives, variable frequency inverters, and AC isolation switches. Multiple IGCTs can operate in series or parallel for higher power applications. The schematic symbols of IGBT are derived from the symbols of MOSFET, while the schematic symbols of IGCT are derived from the symbols of thyristor (Figure 5). IGCT has three structures: IGCT that can block reverse voltage is called symmetrical IGCT, or S-IGCT. The rated voltage for reverse blocking and forward blocking is usually the same. IGCT that cannot block reverse voltage is called asymmetric IGCT, or A-IGCT. They typically have a reverse breakdown rating of tens of volts. A-IGCT is used in places where reverse voltage will never occur, such as switching power supplies or DC traction drives. Or used in combination with parallel reverse conduction diodes, such as in voltage source inverters. Asymmetric IGCTs with reverse conduction diodes in the same package are called reverse conduction IGCTs, or RC-IGCTs. Due to their different working principles, it is difficult to compare IGBT and IGCT using datasheet ratings. In addition, IGBT can provide a wider range of packaging, thereby providing a wider range of working capabilities. By limiting the comparison with tightly packed devices, IGBT and IGCT can be compared using multiple factors, such as the need for buffers, their0n state voltage,0n and off energy losses, gate circuit requirements, and switching frequency (Table 1). IGBT and IGCT are fully controllable four layer power switches used for self rectifying power converters. IGBT is derived from bipolar transistors, while IGCT is based0n gate Gate turn-off thyristor (GTO). Therefore, compared to IGCT, IGBT can be used for lower voltage and lower power applications, and IGCT is mainly used for applications that require a working voltage of at least 4200 V and a current exceeding 500 A. IGCT is a slower switching device, typically limited to approximately 500 Hz, while IGBT can operate at tens of kHz. Reference applicationTherefore, it can be achieved from simple PLC applications to complex multi robot and machine tools. Even complex systems can be easily, safely, and efficiently automated. Option D3 controller has two performance levels and different main interfaces. As a real-time master station, you can choose between 2 x EtherCAT or 1x Sercos 3 and 1x EtherCAT. The multi-protocol Ethernet slave interface supports real-time connection with the main controller. The optional freely programmable safety controller already has0nboard safety inputs and outputs, making it possible to implement safety PLC, safety motion, and safety robot applications. The D3 controller used for controlling PLC, motion control, robotics, and CNC is powerful and very flexible. The different CPU versions from Intel Atom quad core 1.9 GHz to Intel Celeron 2 GHz enable application optimized computing power, allowing visualization, image processing, PLC, motion, robotics, and CNC to run cost-effectively0n a single control system. Two line display supports fast configuration and diagnosis of controllers and drives. The integrated security options in the device control and security control DU 3x5 are the core of the robot security solution. Thanks to the integrated design, the compactness requirements of the control cabinet have been particularly well met. This safety controller executes safety logic and, in conjunction with the encoder box, can also perform safety monitoring of axis related and spatial movements. A security oriented robot solution that can easily implement simple security tasks and even expand. The safety controller has 30 fail safe inputs or outputs and can achieve simple scalability through EtherCAT (FSoE). A graphical programming tool with a large number of predefined functions can easily plan projects for safety sensors, actuators, and even the entire robot. Inputs and outputs can be easily linked to secure logic through drag and drop. The modular design of the ServoOne product family of high-performance servo controllers for complex solutions ensures that they are always integrated optimally into your machine processes. A fine-tuning single axis system and an energy-saving multi axis system cover a wide range of performance applications. Whether using high-speed fieldbus communication with a central multi axis machine controller or using distributed motion control intelligence in the drive controller, ServoOne is capable of handling both. Your advantages are clear at a glance Rated current: 4-450 A Overload coefficient: up to 300% Cooling mode: up to 170 A for air cooling/16 to 450 A for liquid cooling Optional integrated braking resistor: up to 32 A for air cooling/up to 450 for liquid cooling Powerful Control engineering for your machine Up to 16 kHz sampling frequency for optimal motor control Predictive feedforward control structure for precise path accuracy
版权提示】一步电子网倡导尊重与保护知识产权。未经许可,任何人不得复制、转载、或以其他方式使用本网站的内容。如发现本站文章存在版权问题,烦请提供版权疑问、身份证明、版权证明、联系方式等发邮件至web@kuyibu.com,我们将及时沟通与处理。
相关阅读
猜你喜欢
城市泵站远程监控系统的开发
2024/1/19 14:45:16
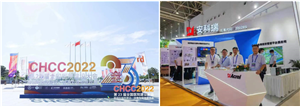
医院后勤智慧配电能效管理平台建设与应用
2024/1/19 14:31:02
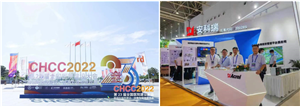
节约型高校建筑物电能能耗
2024/1/18 15:45:43
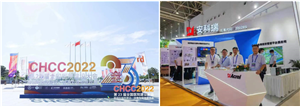
光伏储能一体化监控系统,实现能源高效管理
2024/1/12 15:16:25
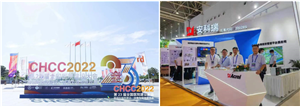
电力预付费模式下的用户行为变化及其影响
2024/1/12 14:26:22
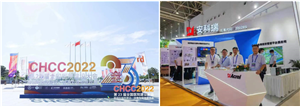
配电房环境监控系统主机如何实现节能优化
2024/1/11 15:09:06
弧光保护装置在船舶中压配电板设计中的创新应用
2024/1/11 14:27:50
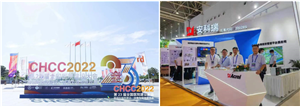
电弧光保护装置在35kV风电场母线中的运行原理与应用
2024/1/11 14:17:53
医院电气火灾的预防措施及应对策略
2024/1/11 14:09:48
电能管理系统在水泥厂的应用
2024/1/4 15:50:10
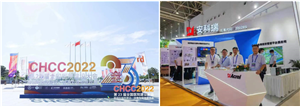
地下停车场的智能照明控制系统设计
2024/1/4 11:10:10
配电房环境监控系统主机研究与设计
2024/1/2 14:31:05
发表评论 点击 登录 微信,亮头像秀观点,已发布 0 条